Cement kiln collaborative disposal technology realizes the “reduction, harmlessness, and resourceization” of garbage, and has achieved good social benefits, environmental benefits and economic benefits. However, due to a large amount of harmful ingredients such as sulfur, alkali, and chlorine in garbage waste, it is enriched in the cement kiln heater system, which causes refractory bricks to be easily eroded, peeled, and damaged. At present, aluminum silicon products in the low -temperature zone of cement rotation kiln, such as silicon -silicon martyrs, anti -peeling high aluminum bricks, and new low aluminum Mo Lai stone bricks, etc., the differences in raw materials and physical and chemical performance are obvious. In this work, compare the alkali corrosion performance of different products above, and combine the analysis of the micro structure and the composition of objects to determine its quality of anti -alkali erosion performance, and then optimize the selection and configuration of cement kiln refractory materials.
Refractory brick selection:
Choose the commercially available Silicon Mulite Brick 1680, Silicon Mulite Brick 1550, anti -peeling high aluminum brick JA, low aluminum mulite brick M55. The physical and chemical performance of the brick is shown in Table 1.
project | Silicon Mulite Brick1680 | Silicon Mulite Brick1550 | anti -peeling high aluminum brickJA | low aluminum mulite brickM55 |
Al2O3% | 67.69 | 63.53 | 80.58 | 60.48 |
Fe2O3% | 1.69 | 1.82 | 1.92 | 1.26 |
SiC% | 7.89 | 6.22 | — | — |
Apparent porosity% | 17.2 | 18.4 | 23.4 | 15.4 |
Volume density% | 2.68 | 2.58 | 2.67 | 2.53 |
Normal temperature resistance intensity/Mpa | 103.5 | 83.9 | 78.4 | 89.1 |
softening temperature/℃ | 1619 | 1575 | 1558 | 1644 |
Anti -heat shock/time | 8 | 5 | ≥15 | ≥15 |
The static method is used for anti -alkali erosion test. Cut the samples with a size of 80 mm × 80 mm × 80 mm from various bricks, drill a cylindrical groove with φ36 mm × 40 mm at the center position, and then cut 60 mm × 60 mm × 30 mm thin plates Cover, drying the groove and lid. Incorporate 20 G’s commercially available chemical pure K2CO3 into each groove, and seal the lid and the groove with fire mud. The entire cricket was dried at 110 ° C in the oven and was placed in an electric furnace at 110 ° C, and kept it in 1100 ° C for 5 h, which was cooled naturally. Evaluate the alkali corrosion performance of the sample by observing the appearance of the sample. Analysis of micro -structure and object composition after the bottom erosion of the bottom, from the bottom of the groove to the bottom of the brick sample to divide the area of 5 mm (see Figure 1), use EDS to analyze the K element content of each region. The X -ray diffraction instrument is used to detect the bottom of the 0 ~ 10 mm area of the 0 ~ 10 mm area.
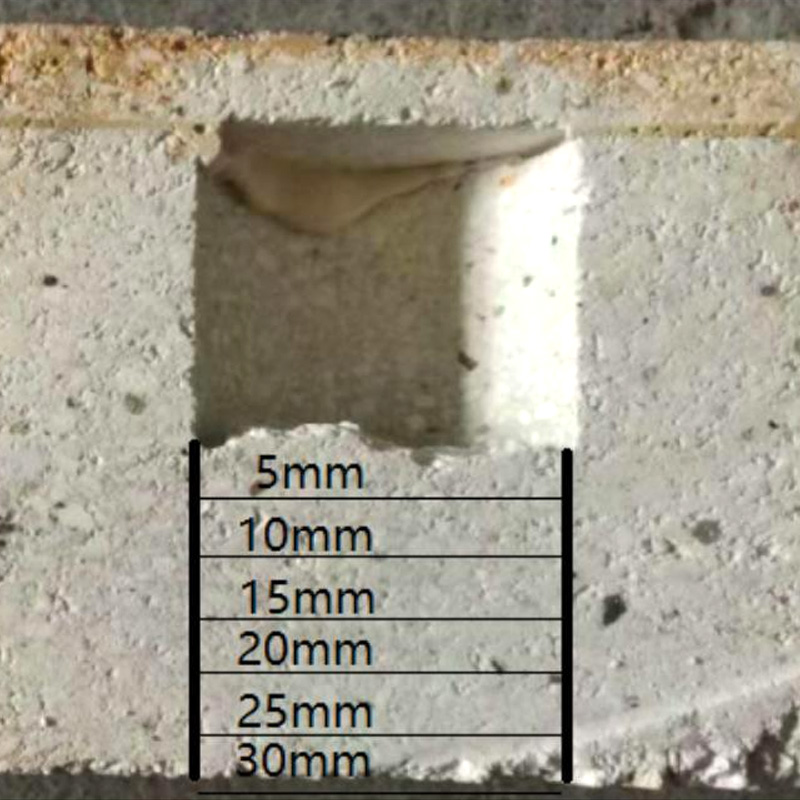
After the erosion of 4 grooves, it was found that: Silicon Mo Brick 1680, Silicon Mo Brick 1550, and Low Aluminum Mo Lai M55 M5 m55 appeared without cracks, with excellent resistance to alkali corrosion; Appearance is relatively poor.
The distribution of K element at the bottom of the groove after erosion
The EDS surface scan is performed on the bottom of the groove to perform EDS surfaces, and the content of the K element is determined as shown in Figure 2. It can be seen from the figure that the distribution status of the K elements of different bricks is very different. Among them, the KE element content of Silicon Mulite Brick 1680 and Silicon Mozi 1550 is consistent with the curve of the content of the K element. The K -element content decreases sharply. After the depth of 20 mm, the K element content is close to 1%(W), and it will no longer change. In the anti -peeling high aluminum brick JA and low aluminum Molai M555, the K -element content distribution curve is similar. Anti -peeling high aluminum brick JA has the highest K -element content at 0, 5 and 10 mm; in the low aluminum mulite brick M55, the highest point of the K element content is 0 and 5 mm. After the K element reaches the highest value in these two sample bricks, as the bottom of the holes is far from the bottom of the holes, the content of the K element has dropped sharply; after the anti -peeling high aluminum brick JA is 30 mm, the potassium content is close to 1%(W), and it will no longer no longer Change; low aluminum mulite brick M55 is close to 1%(W) after 20 mm, and no longer changes.
The alkali corrosion of silicon mulite brick is related to the introduction of silicon carbide and the gas pores of silicon bricks . The oxidized silicon oxidation of silicon carbide at high temperature reacts with potassium carbonate reactions to form glass to form a dense layer at the surface of refractory bricks. It can effectively inhibit the erosion and penetration of the K element, so that the K element is concentrated in the brick surface area. Anti -peeling high aluminum bricks and low aluminum mulite bricks have a high pores. The pores provide a fast penetration channel for melting potassium carbonate. Potassium carbonate enters the inside of the brick along the pores, and some alkali reacts with the brick at high temperature to form mines such as sesame stones or white garnet. The generation of Xiashi or white garnet produces a large volume expansion and causes the brick body to crack. Inside the brick body, decreased with temperature. When the outer surface of the brick is peeled off due to the crack, the temperature of the K -element rich area rises, and the reaction with the refractory material continues to generate the shelters and white garnet minerals, causing cracks inside the brick body. The anti -peeling high aluminum brick with high air perforated rate is higher than the low -aluminum mulite brick tiles with low pores with low pores, and its K element is more enriched in the surface area.
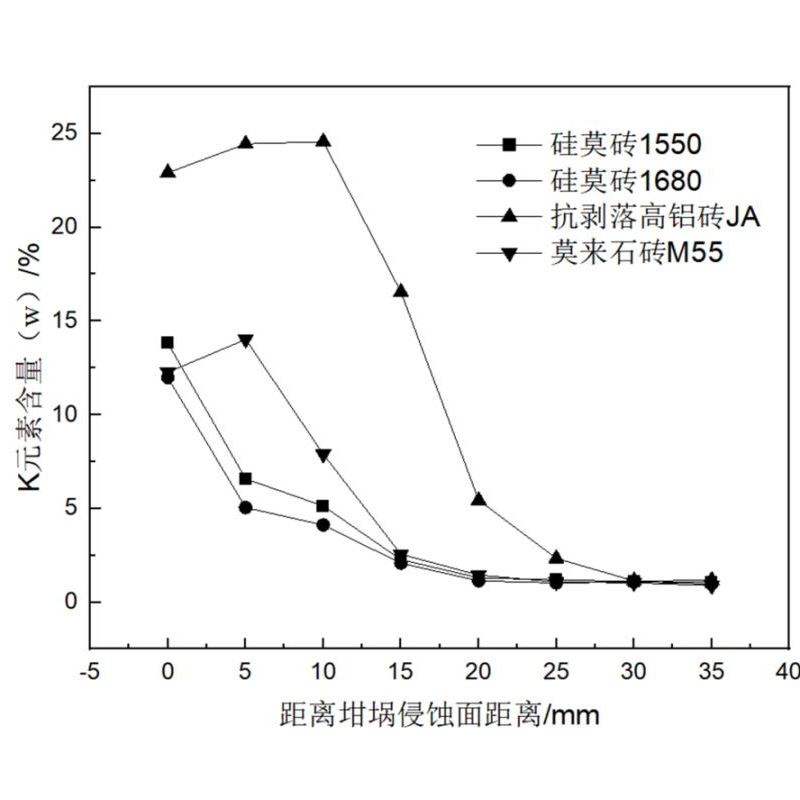
Analysis of the micro structure and phase composition of the 0 ~ 10 mm area of the corrosion layer
Silicon Mulite Brick 1680
For the SEM photo under different times of the 0 ~ 10 mm region of the silicon brick 1680 erosion layer after the alkali erosion. Observation found that the surface structure of the bottom layer of K2CO3 is dense, and cracks in part of the large particles edges are cracks. Observation and seeing: The edges of the alum earth particles in the matrix are eroded significantly, and silicon carbide has not changed significantly.
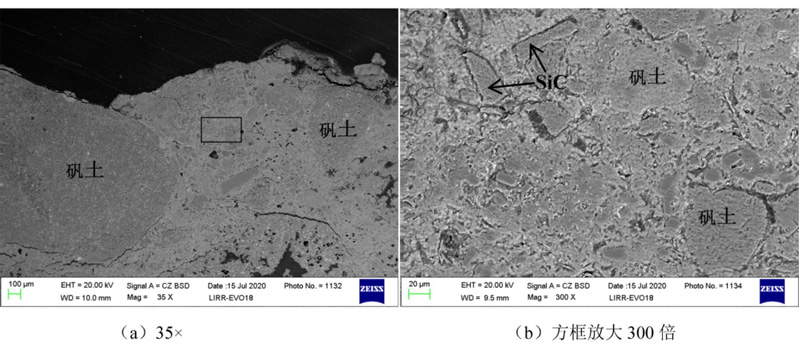
Different multiples Silicon Mulite Brick 1680 erosion layer 0 ~ 10 mm regional micro -structure photos
The following pictures are XRD diagrams in the 0 ~ 10 mm region of Silicon Mulite Brick 1680. It can be seen that its objective composition is mainly Jade, Mulite, and silicon carbide, and the K element exists in the glass phase. It can be seen that the alum soil is easily eroded in the base of silicon bricks at high temperature. The silicon and potassium reactor generated by alum soil and silicon carbide oxidize the liquid phase, the liquid phase filling silicon no brick pores, and the closed refractory brick tiles and the alkali contact area The pores and cracks form a dense layer, which hinders the further penetration of the K element.
XRD diagram of Silicon Mulite Brick 1680 erosion layer 0 ~ 10 mm areas
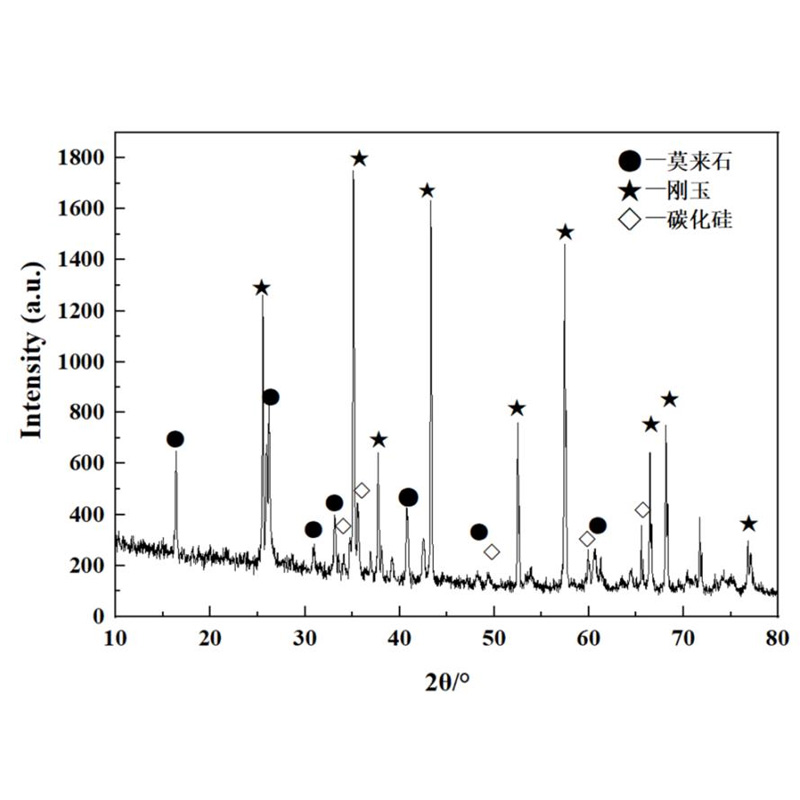
Anti -peeling high aluminum brick JA
The bottom 0 ~ 10 mm area of the groove at the bottom 0 ~ 10 mm area of the groove is shown in Figure 5 after the anti -peeling high aluminum brick JA is eroded. From Figure 5 (a), it is found that the surface structure of the bottom becomes dense, the alum earth particles are eroded obvious, and the particle structure in the matrix becomes not obvious. From Figure 5 (b), the edge of the matrix particles becomes very vague, and the pores or crystal boundaries are filled with a large number of light color new phases. Anti -peeling high aluminum brick JA has a high air hole rate. Potassium carbonate enters the interior of the brick eclipse along the stomach or crystal world, and the depth of erosion is large. Analysis of the objective phase of the corrosion layer was found to have potassium stones for generation (see Figure 6). The production of a large amount of potassium stones causes volume expansion, resulting in a large penetrating cracks produced by anti -peeling high aluminum bricks.
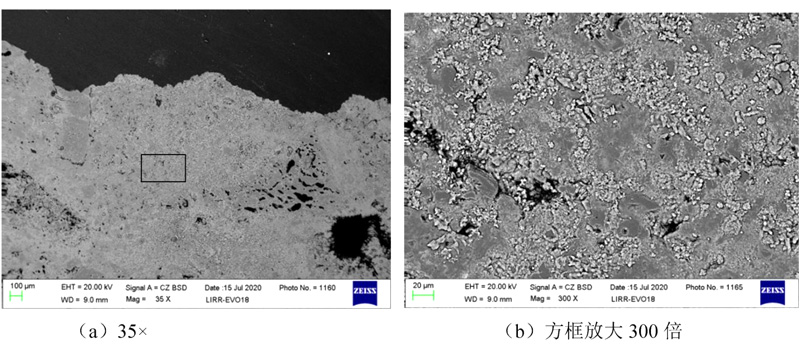
Anti -peeling high aluminum brick JA erosion layer 0 ~ 10 mm area micro structure photos
Low aluminum mulite brick M55
Low aluminum mulite brick M55 alkali is eroded at the bottom 0 ~ 10 mm area of micro -structural photos. See Figure 7. From Figure 7 (a), it can be seen that the surface structure of the bottom layer at the bottom of the low aluminum mulite M55 also produces a small amount of cracks, and the structure has become dense, but it is different from the anti -peeling high aluminum brick. Observation at the high multiple (see Figure 7 (b)) observes that the edge of the mulite also produces a relatively obvious erosion. It can be seen that potassium carbonate also forms a certain erosion and penetration effect on low aluminum mulite bricks. Significant improvement. From the diffraction diagram (see Figure 8), we can see that the main object of the corrosion layer is mulite and a small amount of red pillar stones that have not occurred, and there are also a small amount of potassium sectum stone. The raw materials used in the low aluminummulite brick M55 are mulite ingredients and red pillars as raw materials. The viscosity glass phase; at the same time, the amorphous SiO2 formed by the decomposition of red pillars absorb part of potassium carbonate, which also generates high viscosity glass phase, and is closed by a closed refractory brick to prevent the penetration of the K element. A small amount of potassium carbonate reacts with mulite to generate potassium stones. The amount of potassium Xia Stone is low, and the expansion produced is not enough to destroy the brick structure. Therefore, the low aluminum mulite brick M55 shows good anti -alkali corrosion properties.
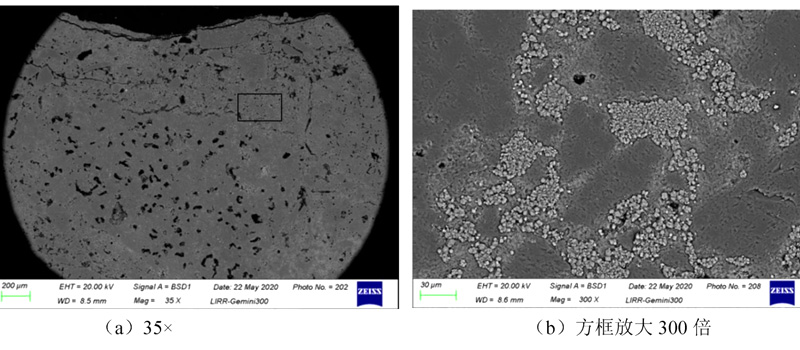
Low aluminum mulite brick M55 erosion layer 0 ~ 10 mm regional micro -structure photos
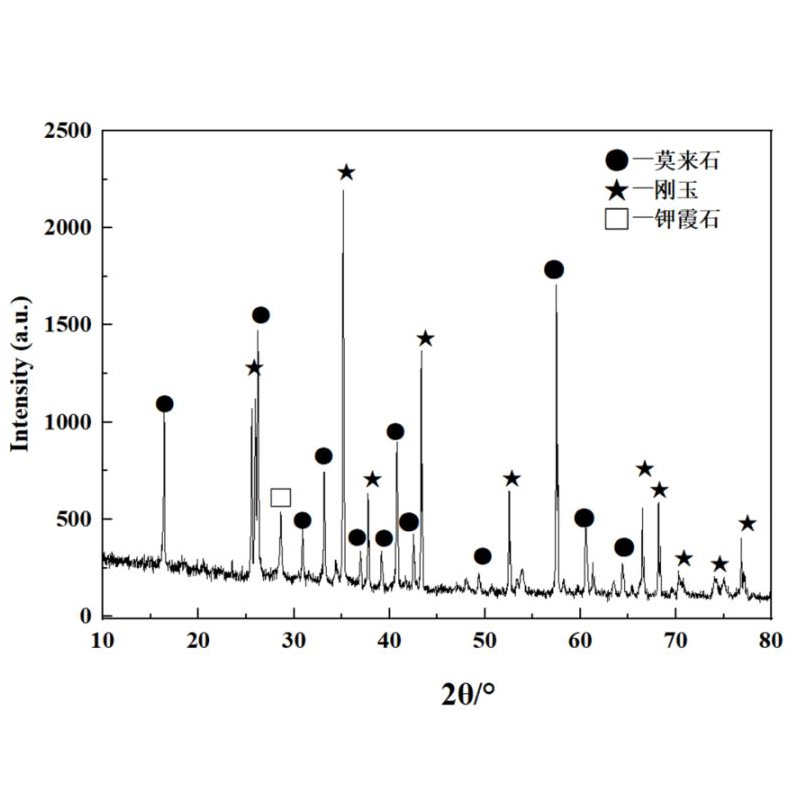
Silicon Mulite Brick 1680 and Silicon Mo Brick 1550 Due to silicon carbide added and partial oxidized into silicon -filled pores, it can significantly reduce alkali erosion and excellent anti -alkali erosion performance. After the alkali erosion test, the K element is mainly concentrated in the erosive surface area. As the distance increases, the content of the K element has decreased sharply. (2) The air pore rate of the commercial anti -peeling high aluminum brick JA is high, the alkali corrosion performance is poor, the depth of alkali erosion reaches 10 mm, and the K element content (W) in the erosion layer reaches 20%to 25%. Xia Shi caused the brick body to crack. (3) Low aluminum mulite brick M55 has a low pores. The average material of the mulite and the structure of red pillar stone raw materials are dense. A certain amount of high silicon amorphous phase in the matrix can absorb alkali to generate high viscosity glass phase. The depth of alkali erosion is only 5 mm, and the amount of potassium stones is relatively small in alkaline erosion, which is not enough to destroy the brick structure. our website:www.yyrefractory.com