Castables are the main type of monolithic refractories. Depending on the adhesive used, the cure formation mechanism can be divided into three types: hydraulic, air-hard, and hard. It is also the most widely used refractory material at present. Although it is very convenient in construction, it has high requirements for objective factors, not only the proportion of configuration, the amount of water added, but also the storage environment and kiln. There are also special requirements before the furnace is fired.
1. Hydraulic castables: Castables with cement as binder require water to participate in the chemical reaction in the hardening process to form cement hardening strength, all of which are hydraulic refractory castables.
Cement is the main factor determining the strength of castables (especially the strength at room temperature), but its refractoriness is relatively low, so after ensuring the necessary strength at room temperature, the amount of cement should be reduced as much as possible. If compactness and structural workability are required, refractory powders can be appropriately added. Reducing the amount of cement is also one of the measures to reduce costs.
During construction, the mixing of high alumina castables with Portland cement, lime, etc. should be strictly prevented. Due to the mixing of two different chemical components to form tricalcium hydrate, the strength is greatly reduced.
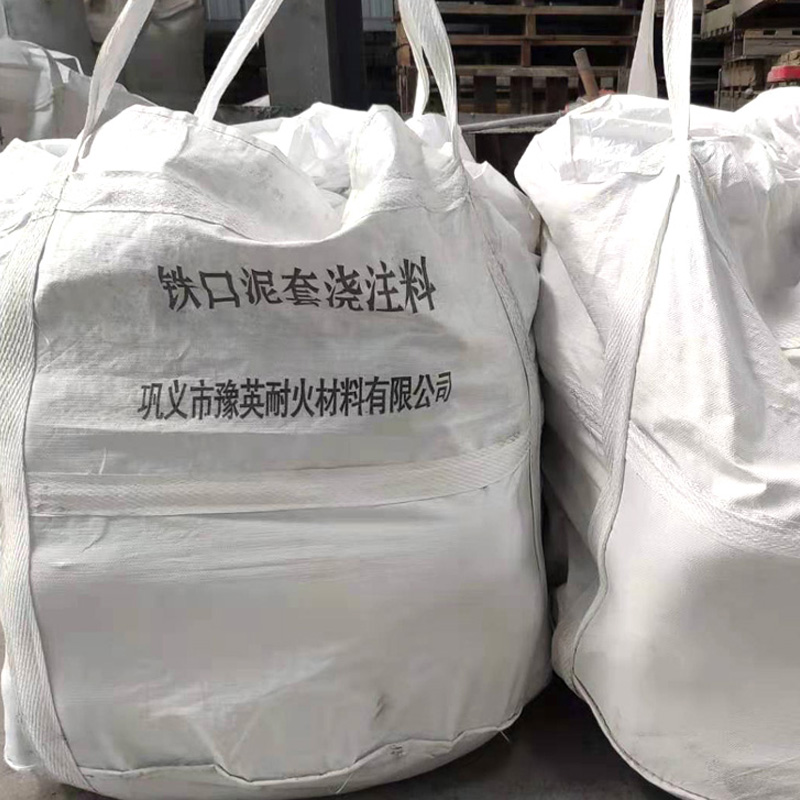
2. Air-resistant castables: This means that the adhesive absorbs CO2 in the air during the curing process, and gradually solidifies and hardens. The commonly used refractory castable is water glass refractory castable.
In addition to high temperature resistance, water glass refractory castables are also resistant to acid and wear, so they are often used as linings for chemical equipment.
The process of hardening water glass refractory castables under natural conditions is very slow, and coagulants (sodium fluorosilicate, high alumina cement, etc.) are added during construction.
The specific steps of using the castable are as follows:
1. This castable is a finished bulk material. It should not be placed in open air and humid places during storage. It should not be mixed with other products.
2. After the construction machine and mould are fully prepared, add the castable according to the capacity of the mixer, add the small bags of adhesive to each bag and dry mix for 5-6 minutes, then add about 13% water bag (6.5kg) to each bag , wet mix for 5-6 minutes before use.
3. The mixed castable should be poured within 30 minutes. If the wet mix has been left for too long, the original installed castable must not be used. Therefore, the template and shaker must be prepared before mixing.
4. The pouring of the lining needs to be kept naturally and can be covered without watering. The initial setting time was 3 hours, and the final setting time was 18 hours before demolding.
The storage of refractory castables must be kept in a roofed or closed warehouse, and cannot be placed in the open air to prevent rainwater and sunlight. When the temperature is high, put it in a cool and humid place. In winter, pay attention to anti-freezing, and be sure to use it up within the shelf life.
After the kiln is built or repaired, before the oven, a layer of plastic film should be covered on the surface of the refractory castable to prevent the surface from curing and cracking. Of course, the film should be removed before the furnace is started.
Before the oven, try to use the local baking method, use wood or charcoal and other fuels to heat up the part of the refractory castable, slowly keep it at 200-300 degrees, and the protection lasts about 6 hours. The function is to completely discharge the water inside the castable. When the state of the ceramic structure appears on the surface, re-ignition can make the service life and service conditions of the refractory castable to be optimal. Our website:https://www.yyrefractory.com.
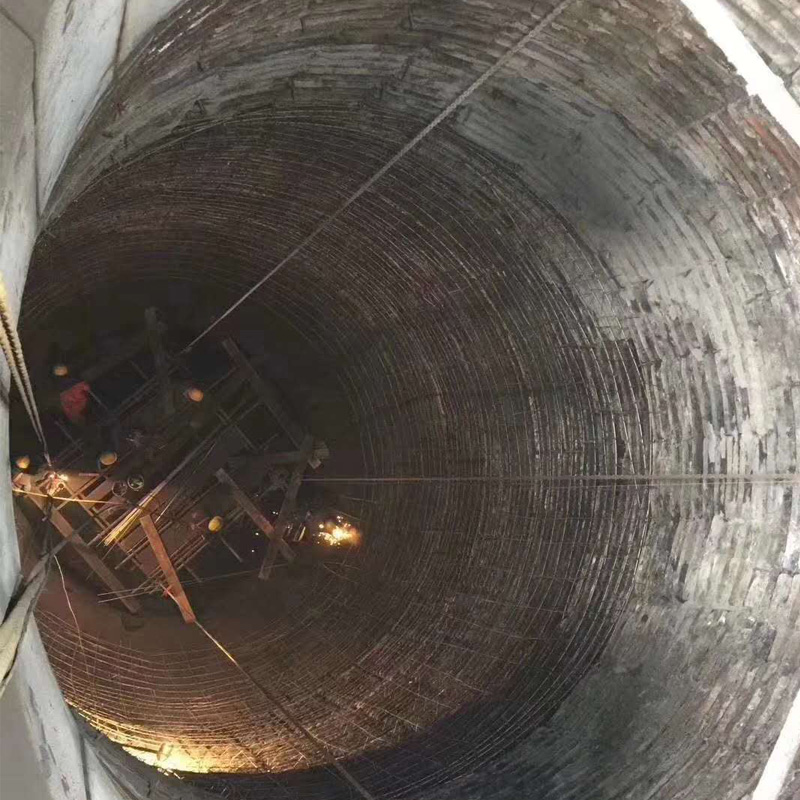